Duct Tape - Through Thick & Thin
Foundation Findings #28 - September 1997
If you're like most like most boaters, your tool kit, tackle box or ditty bag contains an odd assortment of tools, spare parts, fasteners, and "whatzits." The contents may reflect your personal proclivities, your boat's idiosyncrasies or your most recent adventures in marine maintenance.
But if there's one universal item among all boaters' fix-it inventories it's that common commodity among do-it-your-self-ers: duct tape.
Over the years, the BoatUS Foundation for Boating Safety has tested marine products ranging from life jackets to heaving lines and from chart plotters to binoculars.
But this time, as a special service to our members, we wanted to delve into a truly sticky subject, that gray roll we all seem to reach for in a pinch.
Since boaters roll out the duct tape so often for so many applications, we wondered what differences there might be among the various tapes commonly available. Would one brand adhere, resist tearing or seal better than another? For the results of our "ductorial" thesis, stick around.
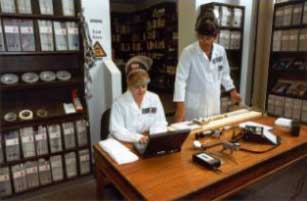
The Little Tape that Could
If you find duct tape useful around your boat, thank bunions. Today's tape stretches back to the 1930's and the cloth surgical adhesive tape developed by manufacturers like Johnson & Johnson and Dr. Scholl's. (See, you had duct tape's first cousin in your first aid kit and didn't even know it.)
With World War II came the need for a waterproof packaging tape to seal ammunition boxes. So the surgical tape troops turned their talent to the war effort and came up with a cloth and nitro-cellulose laminate with a natural rubber adhesive coating. And it came in uniform: olive drab.
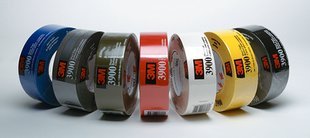
After the war, people began looking for new uses. Then a tape-type from Fort Worth named Harold Potter had an idea. Potter, a distributor for Dr. Scholl's Adhesive Tape, tried the stuff to seal air ducts for the heating and air conditioning industry. And it stuck.
The backing color changed to gray to match tin duct work and later, manufacturers changed the backing material to polyethylene film. Duct tape has been that way, more or less, ever since.
Technically, duct tape is a three-part laminate, bonding under high pressure a polyethylene film, cotton cloth and natural rubber adhesive with hydrocarbon resin as a tackifier.
The Tape Test
We tested six tapes from four manufacturers purchased at random on a shopping spree that included a marine supply store, a home improvement outlet and a we-sell-everything-you-can-think-of drug store.
We ran tests for tensile strength, adhesion quality and pressure resistance, and we added a subjective evaluation of how the tapes stood up to exposure to the elements.
Tape Test Procedures
One convenience of duct tape is that it tears easily, making it ideal for quick application in most situations, without tools. We wanted to asses its tensile strength and adhesive power in straight-pull applications.
To do that, we built an apparatus using a mica laminate surface. Tape samples were attached between a fixed plate and a sliding clamp, and force was applied to pull the clamp away from the plate through a block and tackle.
A recording scale between the fall on the tackle and the sliding clamp measured the force required to break the samples in the strength tests and to pull them loose in the adhesion tests.
For both tests, we cut five 6-inch strips of each product. (For the breaking strength test, we cut the 2-inch wide strips in half in order to accommodate the 50-lb pull limit of our test equipment). We then compared the average reading by brand.
For the pressure test, we assumed hose repair to be the most likely application on a boat and adapted a device used to pressure test engine cooling systems. The unit is pumped by hand and reads air pressure on a gauge calibrated in ponds per square inch (PSI).
We used a one-foot section of 1-inch flexible PVC hose with a quarter-inch hole bored in the middle. With one end blocked and a tape sample wrapped once over the hole, we recorded the pressure required to burst the tape.
Breaking Strength
Tensile strength is a function of thread count of the cloth and strength of each thread. It's expressed in vertical and horizontal threads per inch. The higher the cloth count, the greater the strength.
To test tensile strength, with both ends of the tape secured, we applied pulling force until the sample parted.
Nashua Industrial Grade brand tape proved strongest, breaking at 40.57 lbs.
Adhesion Test
In the adhesion test, we applied a 2-inch by 3-inch section of each sample to our test surface. Then we clamped the remainder in place and applied the pulling force. (We cleaned and dried the surface after each test.)
Manco "Duck" took honors, peeling away at an average of 47.8 lbs. In last place, Tuck Tape pulled loose at 39.1 lbs.
The Tuck brand leaked air at 52.4 psi while the other five began to fail at 24.2 to 34.5 psi. The Tuck tape performed 35% better than the next best, Nashua Industrial Grade.
Actually, we found that with the exception of the Tuck brand, duct tape did not burst under pressure. Rather, air seeped through the tape as it bulged out over the hole and the material separated, more like a slow leak than a blowout.
Exposure
Duct tape breaks down fairly quickly when exposed to the elements. To see if we could draw any useful conclusions on that score, we performed a subjective exposure test.
Using three samples of each, we stuck 6-inch sections to an acrylic panel and left it on the roof of BoatUS Headquarters in the blazing Virginia summer sun, for three weeks.
Assuming the rippled areas, having pulled away slightly from the surface, provide that much less adhesion area, it seems obvious that the thicker the tape, the longer it will last outdoors.
Cleanup
Duct tape adhesive seems to stick around long after the tape itself has disappeared. According to manufacturers, any naptha-based solvent will remove adhesive residue. (lighter fluid will do the trick.) The key is to soften the adhesive with a solvent, then use a plastic ice scraper to remove residue.
When using solvents, experiment first in a hidden area and watch the plastics, painted surfaces and brightwork. And be sure to rinse thoroughly.
Conclusions
- While duct tape certainly has its place aboard your boat for a temporary fix or emergency repairs, it's not for long-term use, except maybe for your boat's ductwork.
- And please, don't use it for electrical insulation. The cotton fabric in most tapes can absorb water and cause a short - or worse. (Use that other ubiquitous tape in your tool box, the black vinyl stuff that's made for the purpose.)
- We learned that three factors affect duct tape performance: cloth count, adhesive coating weight and overall thickness.
- For the boater buying duct tape, it appears the higher the cloth count and the thicker the tape, the better its performance, overall. But here's where the buying decision starts to come unglued.
- For the four brands tested, only one listed thickness on the packaging and none indicated the cloth content or any other specifications beyond the roll length.
- So when shopping for duct tape, the best advice might be to simply look for the thickest available. If you can examine the tape through the packaging, you may be able to judge the fabric count of one as compared to another.
- Otherwise, just the "heft" of one roll in your hand versus another of equal length should give you some indication of grade.
- But if choices are limited and all else fails, just remember, with duct tape, you can always take another wrap.